Por: MAI & LSSBB José Luis S. Ruiz Granados.
Apreciables lectores, en mi publicación anterior comentando acerca de generar competitividad a través del desarrollo de estrategias Lean Six Sigma enfocadas en la solución de problemas potenciales; sin embargo, este direccionamiento es con base en un ambiente de excelencia operacional en el cual la innovación y la mejora continua se aplican de forma estandarizada en todos los proceso de transformación y servicios (Fig.1)
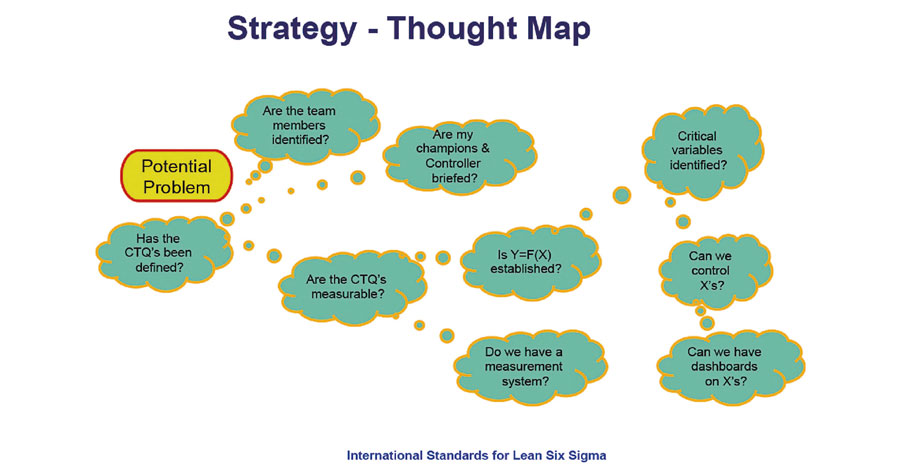
Y también vimos las metodologías a aplicar en este proceso de mejora continua (Fig. 2):
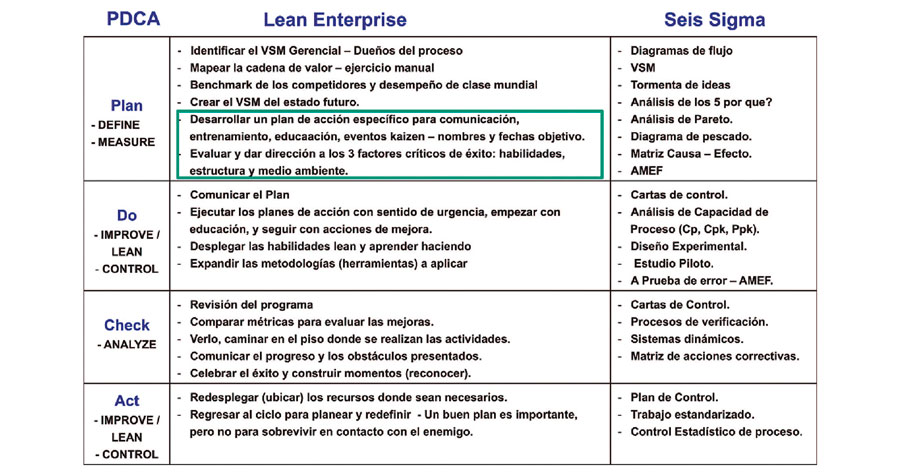
En esta ocasión, abordaremos en este artículo, que dividiré en dos partes A y B, siendo esta la parte A, y tomando como referencia la situación actual de nuestro sector industrial, trataremos el camino para la solución de problemas reales en nuestro día a día a través del trabajo en equipo y la implantación de aportación de valor para la organización, con el objetivo de que el proceso fluya, por lo que lo comentaremos en una metodología muy importante conocida como Kaizen, misma que desde una perspectiva personal y a que la he estado aplicando en los procesos en los cuales me he involucrado para mejorarlos, considero que debe estar, como parte fundamental, dentro de las competencias laborales que en la actualidad se requiere tener cubiertas como parte del perfil de puesto, tanto de los profesionistas como de los operadores, para la solución de problemas en la mejora de los procesos (Fig. 3), y es la base para implementar otras iniciativas tales como 5S, TPM, SMED, KANBAN, AMEF, Poka Yokes o dispositivos a prueba de error, VSMa y VSMf, entre otras más (Fig. 2).
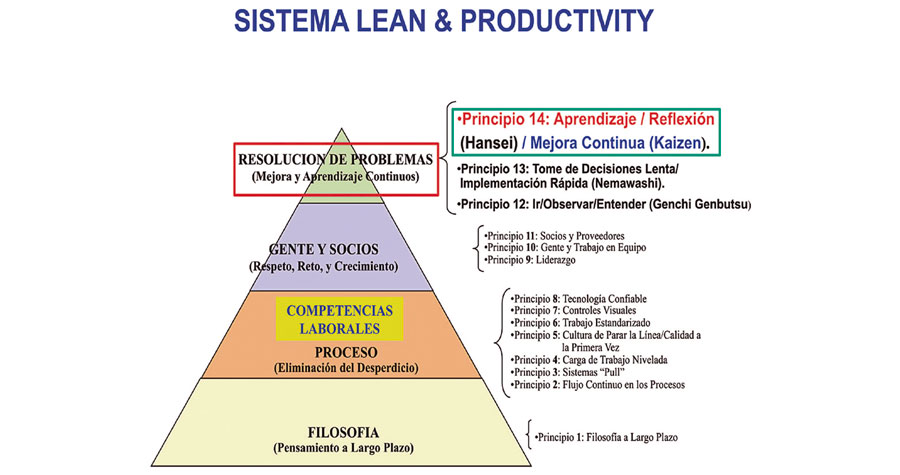
Por lo tanto, se hace necesario e indispensable integrar al personal que opera y vive los procesos todos los días, cuyo expertise es básico y su conocimiento técnico es importante para la solución de problemas. Con este enfoque, la metodología Kaizen como procesos-gente operativa integral, es básica, con pleno conocimiento técnico del proceso, liderados por sus facilitadores del conocimiento, título que debe ser acreditado por el supervisor del área operativa en la generación de valor de su perfil de puesto, por lo que ahora el supervisor como tal está siendo obsoleto, ya que desde esta perspectiva la adición de valor se ve limitada, puesto que no sólo debe concretarse a verificar lo que los operadores deben estar realizando muy bien sin vigilancia alguna, por lo tanto debe plantear el hecho de realizar eventos Kaizen como concepto de mejora y solución de problemas, en la que todos y cada uno de los integrantes del equipo ejerzan su liderazgo, creatividad e innovación en la aplicación de esta metodología (Fig. 4).
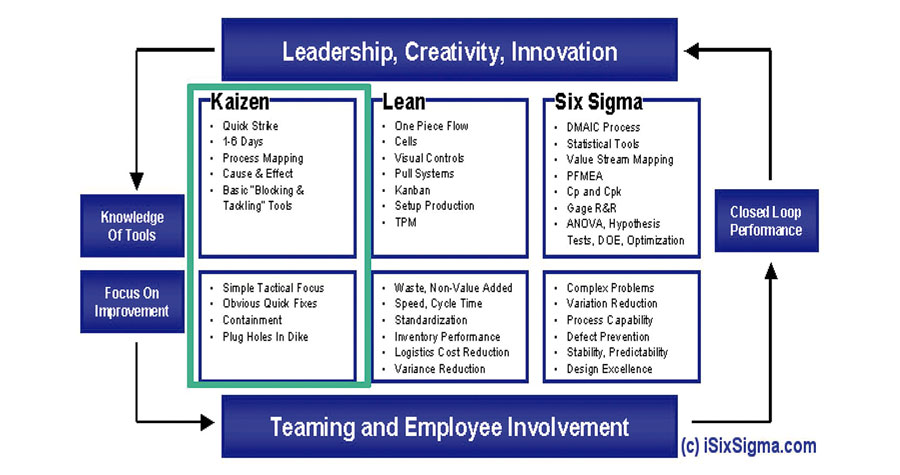
Por consiguiente, debe formar parte de las actividades diarias de los operadores dentro del proceso operativo, ya que es en donde nace la calidad de los productos y servicios, y con base la Nom-059-SSA1-2015 en su sección 9.1 Generalidades “La validación de procesos no es un evento puntual en el tiempo, sino que involucra un enfoque relacionado al ciclo de vida del producto, el cual debe considerar que la variabilidad es una característica intrínseca de los procesos de fabricación; conocer esta variabilidad, controlarla y analizar el impacto en la calidad, seguridad y eficacia de los medicamentos debe conducir a los procesos de mejora continua” (Fig.5).
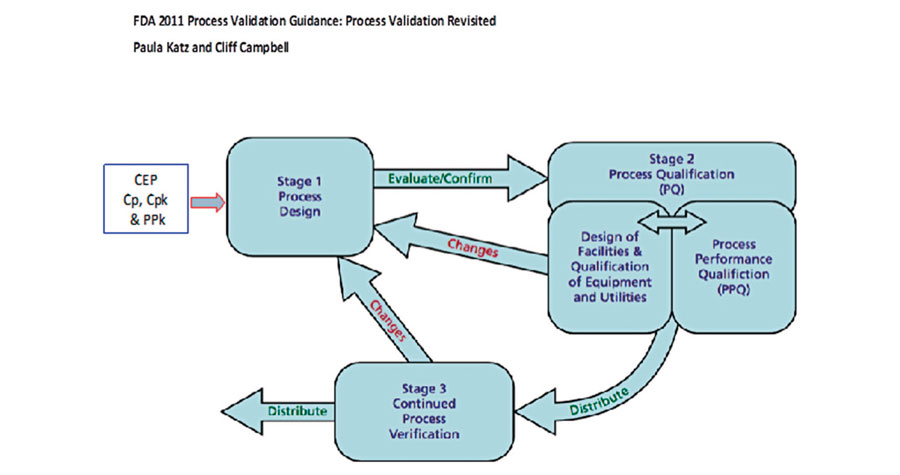
En la que el cumplimiento de las tres etapas de la validación de los procesos, demostrando el mantenimiento del estado validado en todo el ciclo de vida y con base en la verificación continua del proceso en la etapa 3 (incisos 9.9.2.3 y 9.9.2.3.4), esta mejora de procesos, en la práctica, los hemos estado realizando a través de eventos Kaizen (Fig. 6).
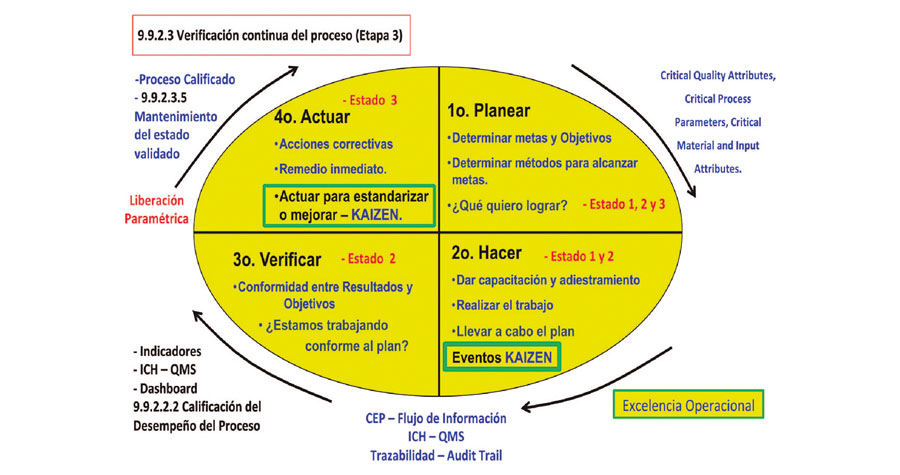
Una vez seleccionado el proceso a mejorar y manteniendo el estado validado, se aplica la metodología DMAIC relacionada al SCORE en Kaizen, se realiza el evento Kaizen (Fig. 7), utilizando y completando los formatos establecidos en el SCORE, así como aplicando la metodología Yellow Belt para solución de problemas.
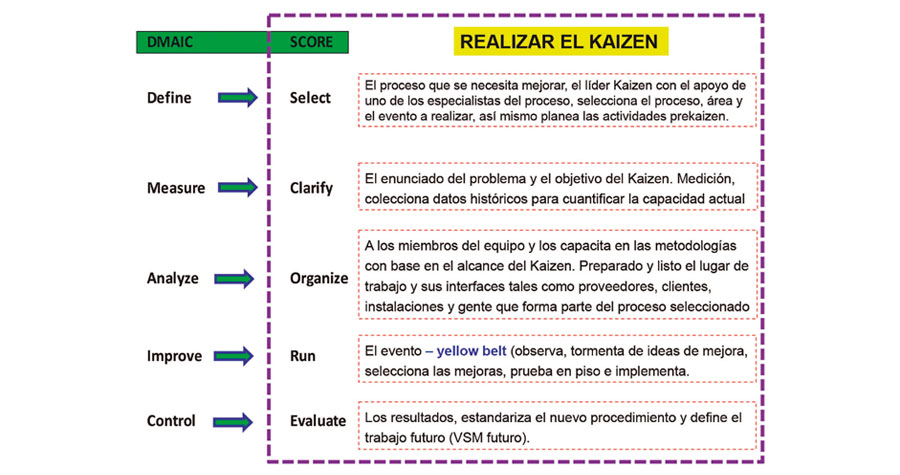
Finalmente, se estandariza este proceso de mejora continua, se documenta el evento, se actualizan los PNO´s involucrados y se integran al SGC (Sistema de Calidad) los nuevos PNO´s, y se definen las métricas necesarias relacionadas a cuantos eventos Kaizen requerimos realizar en un periodo determinado y lo integramos a la evaluación de desempeño del personal de la planta, con los resultados obtenidos y en cumplimiento de los objetivos de cada evento Kaizen (Fig. 8).
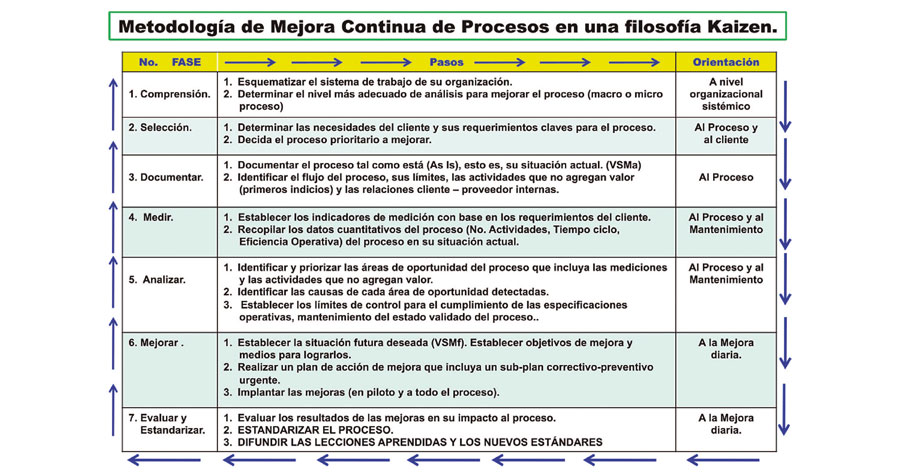
Convirtiéndose en un proceso continuo que no tendrá fin, en línea con el cumplimiento Normativo NOM-059-SSA1-2015 y normas internacionales, generando la ventaja competitiva que toda empresa o laboratorio requiere para llegar a ser líder del sector, en la que, entre otros trabajos a realizar, el supervisor, ahora facilitador de conocimiento, deberá estar en cumplimiento de las acciones llevadas a efecto en los Kaizen y el nuevo sistema de trabajo, alineando sus actividades en función del diagrama de Ishikawa para prevenir potenciales fallas, esto es CAUSA – EFECTO, y mantener los beneficios de los eventos Kaizen, que entre otros, están bajos costos de operación, máxima calidad y entrega rápida, sistemas ágiles en cumplimiento normativo con apoyo de la Tecnología DATA 4.0 y dispositivos electrónicos en las máquinas y líneas de acondicionado que migran la información a pantallas digitales de forma tal que se actúe de manera inmediata (Fig. 9).
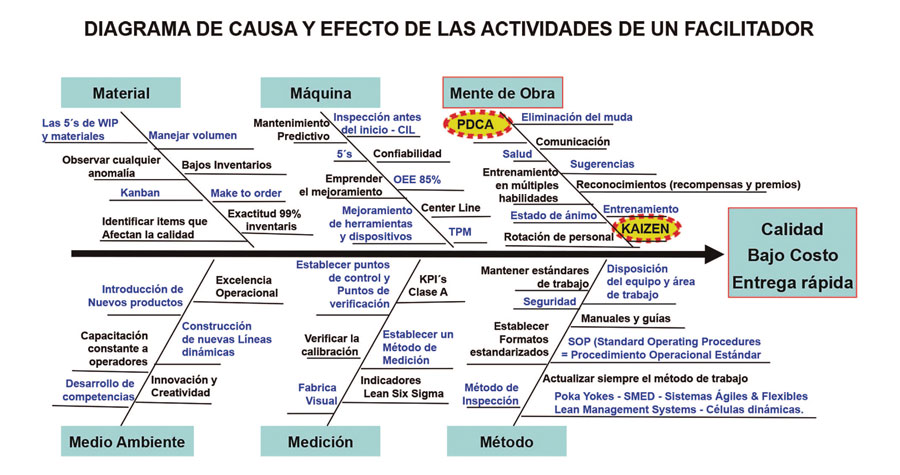
Estoy consiente de que nos faltó explicar algunas tópicos que utilizamos en esta sección, por ejemplo el SCORE, por lo que continuaremos con esta línea y los comentaremos en la segunda parte B que seguramente aparecerá en el siguiente número de la revista enFarma. ¡¡Hasta la próxima!!